Waterjet Cold Cutting
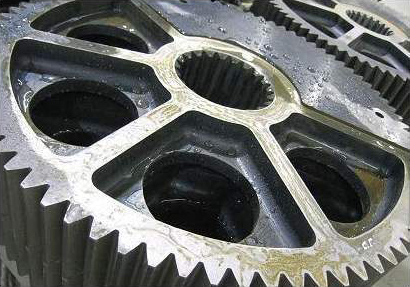
we are engaged in offering waterjet cutting service. In this no damage is caused to the metal because this is a cold cutting process. In this process, materials with low melting points are precisely cut to provide them with smooth edges. The materials that are cut with process, includes synthetic foam, heat treated hardened metals, ceramics, carbides, composites. The material to be cut is not heated, ensuring no structural changes or no heat-affected zones (haz) that can affect the metallurgic properties of the materials being cut.
In this process, water jet cutting force is directly applied on the top of the work piece, resulting in low side –to –side cutting force. The design cycle is very short and changes can be made quickly as the design of the material to be cut goes directly from the CAD system to the waterjet cutter. The designs of different materials can be cut as per the specifications mentioned by our esteemed clients.
Advantages :
- No vibration on the parts to be machined
- Saves on costly Jigs and fixtures or work holding devices to hold the work piece
- Frail parts and parts with a long length to width ratio can be cut with relative ease
- Eliminates the need and cost of drilling starter holes
- Eliminates the possibility of chipping of corners
- Brittle materials can be cut
- Those parts which do require further processing are easier to machine and finish
- Quick parts –From Concept to part production, the short turnaround time also offers many advantages like saving on shifting materials for secondary operations
- Minimum hole size of 2.5mm diameter. Possible to cut random contours, very fine tabs and filigree structures
- No heavy burrs are produced by the abrasive waterjet. Parts can often be used directly without de-burring.